High Fire Glazes
Grid sets that contain glazes suitable for high fire.
These sets contain glazes that are suitable for around 1300 deg C. or around cone 10... plus or minus 50 deg C at least, or a couple of cones. Many of the glazes on these tiles will be better at higher or lower firings, to be determined by the experimenter. Although there is usually a best firing range for a particular glaze, there is no best temperature for any grid tile; any grid may be fired over a range of at least 100 deg. C, and at different temperatures, different glazes will reach their best result.
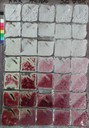
Brantford Chrome/Tin Red
Deconstructing Ron and John's Raspberry Glaze. It can be quite interesting on dark clay. The variation of alumina and silica provided by the grid allows one to choose the most interesting combination for your materials, clay and firing. It is obvious from the tile that these reds do not like high alumina. This tile fired to Seger cone 7 (about Orton cone 8) in oxidation at the Heide workshop in Germany, 2008.
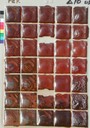
Iron/Bone Ash Red Set
Fired to Orton cone 10 in oxidation at the workshop at Keramikos in Haarlem, Netherlands, 2008. This set shows how the combination of iron oxide and bone ash can make some rich iron-red colours, with interesting small crystal development in many of the glazes.
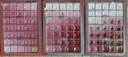
HaarlemCrSnRed^Comparison
Temperature comparison from cone 4 to cone 10 showing some chrome/tin red glazes. At the firing temperature rises, the high alumina glazes (across the top of the tiles) lose the red colour from the chrome/tin combination.
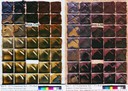
Clay Body Comparison
Comparison of the same set of limestone glazes on a white body and an iron-y body. The set is the Standard Limestone Set, all with 5% red iron oxide, and fired under identical conditions to cone 10 in Reduction.
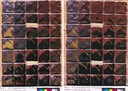
Temperature Comparison
Comparison of the same set of limestone glazes fired to Orton cone 10 and cone 12. The set is the Standard Limestone Set, all with 5% red iron oxide, and both applied to the same iron-y clay body.
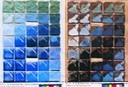
Clay Body Comparison 2
Comparison of the same set of limestone glazes on a white body and an iron-y body. The set is the Standard Limestone Set, all with 0.5% cobalt carbonate and 5% titanium dioxide, and fired under identical conditions to cone 10 in Reduction.
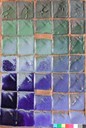
LA-CoTi^7+ox1200px.JPG
A combination of cobalt and titanium produces matt greens with the right amount of alumina in the glaze. For high-firing, this green can be obtained by putting cobalt and titanium (often as rutile) into a shino-type high feldspar (or nepheline syenite) glaze. To get it to mature at mid-fire we can add frit to the set of fluxes and additives, and construct a grid to find where it occurs at the lower temperature. To go from stoneware (e.g. ^ 9 or 10) down to mid-fire (e.g. ^ 5 or 6) firstly enter the original flux and additive set (names and amounts) into the Calculation Page. Now add frit to the flux set and by trial and error, recalculating each time, find what number you need to enter in Row 2 to give 30% frit in the corner C glaze (glaze 31) on the resulting recipe sheet ("35 Recipes for the Set"). You then produce a grid from the corner glazes provided where it says: "Corner Glaze Calculation - Batch Recipes for Volumetric Blending". Once the set is fired it will show where the green occurs with the new set of fluxes. Different frits will give different results; the frit lowers the maturing point for all the glazes in the set by brute force.